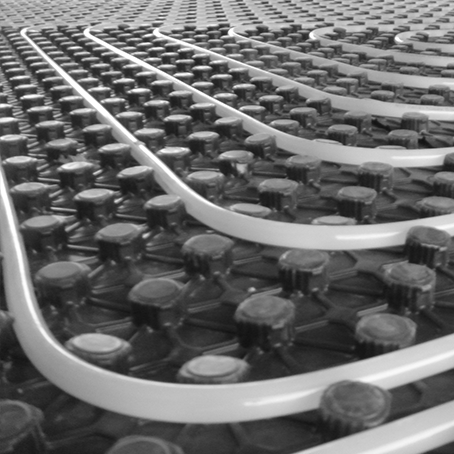
PAVIMENTI RISCALDATI
Il massetto, elemento fondamentale nel dimensionamento di un solaio, nel tempo ha subito un processo evolutivo garantendo prestazioni impossibili da eguagliare con un tradizionale sabbia e cemento e in grado di soddisfare il progettista più esigente. Nel caso di sistemi di riscaldamento a pannelli radianti, l’efficienza degli impianti a pavimento è strettamente legata al sottofondo. Il massetto autolivellante è definito “ad alta conducibilità termica” causa il suo stato molto fluido che avvolge completamente le serpentine compattandosi senza spazi vuoti attorno ad esse. Potendo ridurre di oltre 1 cm lo spessore del massetto, è evidente che con massetti autolivellanti l’impianto a pavimento può funzionare con rese ancora maggiori. Tra le due tipologie di massetto autolivellante, base cemento ed anidrite, quello a base anidrite migliora notevolmente la conduttività avendo un valore di conducibilità termica λ molto più elevato. Complice la sua consistenza semi liquida dovranno considerarsi alcuni accorgimenti basilari qui sotto riportati.
PRESCRIZIONI TECNICHE OBBLIGATORIE
UNI EN 1264-1-2-3-4-5
Norma Italiana che regolamenta gli impianti di riscaldamento a pavimento, entrata in vigore (con ultimo capitolo nr. 5 ottobre 2008) nell’agosto 2001. Pertanto Norma che impone caratteristiche e direttive improrogabili. La norma si applica agli impianti di riscaldamento a pavimento alimentati ad acqua calda, Essa specifica i requisiti uniformi per la progettazione e la costruzione di strutture riscaldanti a pavimento per garantire che l’impianto di riscaldamento sottostante sia idoneo alla particolare applicazione. La norma specifica soltanto i requisiti particolari che dipendono dal riscaldamento a pavimento. Non è applicabile agli altri elementi che compongono tutte le strutture a pavimento (riscaldanti o meno). La norma specifica inoltre come dovranno essere: base di supporto, strati di isolamento, striscia perimetrale, strato di protezione, tubazioni, ancoraggio dei tubi, strati di supporto, strati livellanti, giunti, misure di protezione, posa, prova di tenuta, avviamento dell’impianto.
I pannelli radianti di riscaldamento/raffrescamento a pavimento potranno presentarsi con due diverse tipologie. In entrambi i casi lo spessore del getto varia da un minimo di 5 cm ad un massimo di 7 cm (generalmente 2,5-3 cm di intasamento a livello serpentine oltre almeno 3 cm sopra la serpentina o funghetto come stabilisce la norma EN 1264-4)
a) Con semplici pannelli di polistirene e serpentina posata su di essi. In questo caso si dovrà verificare che i pannelli siano ben accostati fra loro senza spazi vuoti fra l’uno e l’altro (meglio se con giunzioni di tipo maschio/femmina/addentati) e che le serpentine siano ben fisse ad esso tramite l’utilizzo di apposite graffe, in ragione di n. 1 ogni 30 cm, intensificandone la ragione in prossimità delle curve a 180 gradi onde evitare rischi di “galleggiamento”delle stesse. I tagli dei pannelli sul perimetro dovranno essere particolarmente curati, sigillandoli accuratamente. Il progettista deve altresì prevedere la posa di una buona bandella perimetrale comprimibile di spessore 8 mm ed altezza 10 cm con raccordo parete/pannello in polietilene onde evitare percolazioni di autolivellante sotto i pannelli, avendo cura di sigillare con nastri resistenti all’acqua il raccordo con il pannello e di dare alla bandella continuità senza interromperla sui telai delle porte e contro le soglie in marmo esterne ed interne. I giunti perimetrali sono assolutamente indispensabili, sia per assorbire le dilatazioni meccaniche che per isolare termicamente ed acusticamente il massetto radiante dalle pareti statiche dell’immobile. Pertanto, devono essere posizionati su tutto il perimetro di ogni elemento strutturale verticale (muri, colonne, caminetti, scale, ecc.). Sono provvisti di un lato adesivo che ne facilita l’installazione (in caso di
b) necessità è possibile utilizzare anche chiodi o graffette) e di un foglio in polietilene, utile per evitare l’ aggrappaggio del materiale (massetto radiante) con la soletta grezza. Negli angoli e in corrispondenza degli spigoli delle pareti incidere il giunto con un taglierino per la metà dello spessore al fine di migliorarne il contatto con le murature UNI EN 1264-4 PAR 4.2.2.2.In caso di interruzione del pannello di supporto serpentina a causa di tubazioni che fuoriescono parzialmente dal massetto alleggerito, si dovrà prestare molta cura alla sigillatura dei supporti tagliati, posando eventualmente un ritaglio di polietilene da un pannello tagliato all’altro, evitando in tal modo che il massetto autolivellante entri a contatto con supporti o superfici che possano innescare un rapido assorbimento d’acqua dall’impasto.
c) Con pannelli “a passo obbligato” (funghetto). In tal caso valgono le medesime regole sopra esposte. In tutti i casi la serpentina dovrà essere “messa in pressione” con acqua prima del getto. Il progettista dovrà inoltre attenersi alla dislocazione dei giunti di dilatazione considerando la buona regola di interrompere la continuità del massetto nelle passate delle porte e in ogni situazione in cui vi siano restringimenti/allargamenti di superficie e a delimitazioni di campiture massime di mq. 50 (valido solo per massetti autolivellanti cementizi e non base anidrite). UNI - EN 1264-4 PAR 4.2.8.4 “ La modalità con cui i giunti di dilatazione vengono scelti e realizzati, deve tener conto oltre ai limiti imposti dalla normativa vigente (sulle soglie delle porte; superfici maggiori a 40 m2; locali con forma regolare e rapporto massimo dei lati di 1/2; superfici con lati maggiori agli 8 m; anche dalla natura del massetto, dal suo spessore, dal tipo di rivestimento finale di tutte le strutture portanti. Tutti questi fattori ci portano a distinguere:
• Giunti di movimento strutturali (o di movimento) devono essere realizzati prevedendo di dividere l’impianto nella sua integrità, rivestimento compreso. Nel caso specifico in cui la tubazione attraversa il giunto, dovrà essere rivestita con una morbida guaina isolante (spessore 6 mm) per un tratto di almeno 20 cm per parte.
Le eventuali reti di armatura dovranno essere interrotte per non avere continuità sul giunto.
• Tagli del massetto per contenere i fenomeni da ritiro e pilotare le fessurazioni del massetto. La realizzazione avviene posando specifici profili (in cartone o polipropilene) in modo da realizzare tagli che definiscano superfici variabili tra 12 e 40 m2 .
• Tagli del pavimento da realizzarsi per frazionare e meglio annullare tutte le spinte dilatatorie che si verificano in grandi superfici con massetto continuo. Il vantaggio sarà quello di avere stabilità e sicurezza del rivestimento finale.”
È buona norma inoltre l’impiego di una rete leggera (zincata, quindi protetta dalla corrosione degli agenti chimici presenti nel cemento, o di plastica) su tutta la superficie, di diametro variabile tra i 2 e i 6 mm con maglie 5x5 o più fini se di plastica, facendo attenzione ad interrompere la continuità in corrispondenza dei giunti di dilatazione (valido solo per massetti autolivellanti cementizi e non base anidrite). In tutti i casi i pannelli di supporto serpentina dovranno appoggiare bene in piano sull’alleggerito sottostante evitando che si possano muovere durante il getto e/o fissandoli al massetto sottostante con appositi collanti.
Il massetto autolivellante è particolarmente indicato per i sistemi di riscaldamento a pavimento, complice il suo stato semi liquido che avvolge la serpentina uniformemente senza vuoti d’aria creando nel contempo una trasmissione di calore costante su tutto il massetto. Normalmente lo spessore del getto è di 5,5/6 cm, per tale motivo bisognerà sempre considerare un sovrapprezzo rispetto al getto in condizioni normali.
COSA BISOGNA EVITARE
Che il massetto autolivellante in quanto molto fluido, possa crearsi un varco fra le giunzioni dei pannelli, nel perimetro o nelle interruzioni del pannello, sollevandoli dal piano di posa.
Che le graffe di fissaggio delle serpentine non siano in numero congruo o che non siano ben fisse al pannello creando elevato rischio di galleggiamento delle serpentine.
Che le serpentine prima del getto non siano in pressione con acqua.
Che i pannelli non siano ben fissi e inamovibili al fondo sottostante.
Che la rete di armatura non sia ben legata alla serpentina e che non venga interrotta in prossimità dei giunti dilatatori.
Che l’installatore non posizioni gli appositi giunti dilatatori e non preveda una corretta posa della bandella perimetrale.
Di porre in contatto i pannelli di polistirene con le pareti, interponendo fra di essi una bandella comprimibile.
PRESCRIZIONI DI RISCALDAMENTO INIZIALE
I massetti devono essere riscaldati prima di posare il rivestimento finale, secondo quanto prescritto dalla norma UNI EN 1264-4. La procedura di primo avviamento del riscaldamento serve per asciugare il massetto e per scaricare le tensioni nel massetto stesso più rapidamente; per tale motivo anche un massetto asciugato naturalmente va riscaldato prima di applicare un rivestimento. Il tempo di asciugatura dipende dallo spessore del massetto, dalla temperatura di mandata, dalle condizioni ambientali (temperatura e umidità dell’aria) nonché dalla ventilazione.
I primi due giorni dopo la posa il massetto va protetto da correnti d’aria. Un riscaldamento senza ventilazione degli ambienti rallenta notevolmente il processo di essiccamento del massetto, il che significa spalancare completamente le finestre e le porte per creare corrente d’aria e non basta quindi aprirle semplicemente. Perciò ricordarsi di ventilare periodicamente! Anche la presenza di materiali da costruzione sopra il massetto ne rallenta l’essiccamento.
Iniziare il ciclo di riscaldamento dopo 7 giorni dal getto (massetti base anidrite) o dopo 21 giorni (massetti cementizi)
La temperatura di mandata iniziale dovrebbe corrispondere più o meno alla temperatura superficiale del massetto, in ogni caso non essere inferiore a +15°C e va mantenuta per 3 giorni
La temperatura di mandata massima (45-50 °C) deve essere mantenuta per un tempo complessivo di almeno 7 giorni senza interruzioni notturne
La temperatura va poi abbassata progressivamente di max. 10°C al giorno.
Dopo l’operazione di riscaldamento descritta non è detto che il massetto abbia raggiunto il contenuto di umidità necessario per poter procedere alla posa del rivestimento. Per tale motivo sono assolutamente necessarie delle misure di umidità con un igrometro a carburo.
Le informazioni contenute in tutte le pubblicazioni con marchio Pancotti Pavimenti® hanno carattere esclusivamente esemplificativo ed indicativo. I dati e le indicazioni riportati nel presente catalogo possono subire variazioni in qualsiasi momento senza preavviso. Il committente ha l’obbligo di verificare le informazioni, di realizzare scelte progettuali in base alle proprie conoscenze, adeguandosi alle normative vigenti apponendo la verifica scritta di un progettista autorizzato.